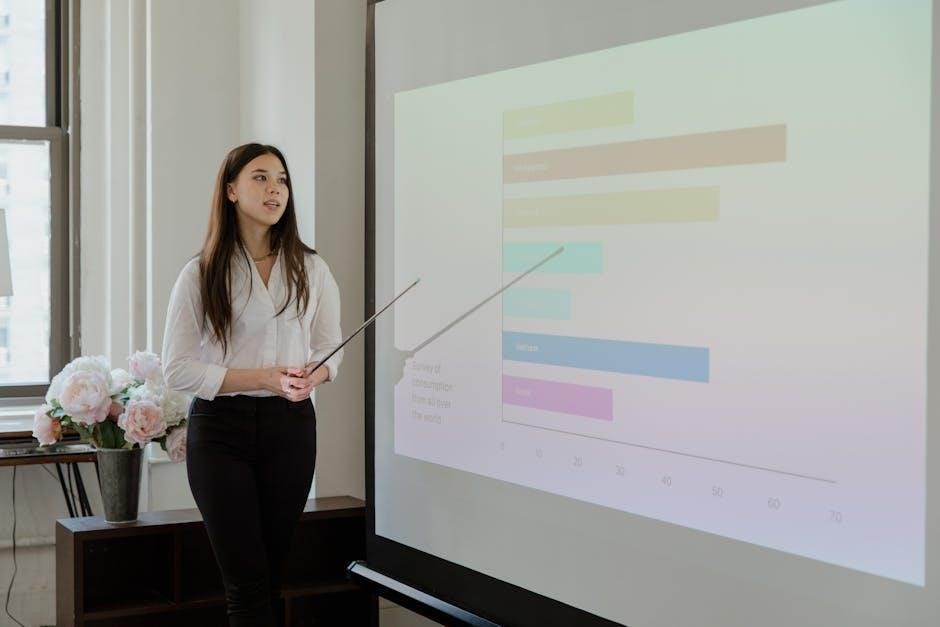
tig welding settings chart pdf
TIG Welding Settings Chart PDF: A Comprehensive Guide
TIG welding demands precision. A comprehensive guide, especially in PDF form, offers welders essential charts. These charts outline parameters, including amperage, gas flow, and electrode selection, crucial for achieving optimal weld quality across various materials and thicknesses.
TIG welding, or Gas Tungsten Arc Welding (GTAW), is a process requiring precise control over numerous variables. Parameter charts are invaluable tools, especially when accessible in PDF format for convenient reference. These charts provide starting points for essential settings like amperage, voltage, and gas flow, tailored to specific materials and thicknesses. They streamline the setup process, helping welders achieve consistent and high-quality welds. Understanding how to interpret and apply the information within these charts is fundamental for both beginner and experienced TIG welders, ensuring optimal performance and minimizing potential errors during the welding process.
Understanding Essential TIG Welding Variables
TIG welding success hinges on mastering key variables. Amperage, voltage, gas flow, and travel speed dramatically impact weld quality. Parameter charts help welders navigate these variables, providing a foundation for achieving optimal results with different materials.
Material Type and Thickness Considerations
Material type significantly influences TIG welding parameters. Mild steel, stainless steel, and aluminum each require distinct amperage settings, gas mixtures, and techniques. Furthermore, material thickness dictates amperage. Thicker materials necessitate higher amperage to achieve adequate penetration. Reference charts typically provide amperage ranges based on both material and thickness. For example, a chart might recommend a specific amperage range for welding 1/8-inch mild steel versus 1/4-inch mild steel. Similarly, aluminum often requires a “hot and fast” approach, demanding higher amperage and faster travel speeds compared to steel. Always consider the material and its thickness.
Shielding Gas Selection: Argon vs. Helium
Shielding gas selection is crucial in TIG welding. Argon is commonly used, especially at lower amperages, providing stable arc and preventing oxidation. Helium, being lighter, offers deeper penetration and is beneficial for thicker materials or when welding aluminum. Helium’s higher thermal conductivity necessitates increased flow rates compared to argon. Some applications utilize a mixture of argon and helium to achieve a balance of arc stability and penetration. Choosing the right gas or mixture depends on the material being welded, its thickness, and the desired weld characteristics. Proper gas flow is essential for effective shielding.
TIG Welding Parameter Charts: Mild Steel
TIG welding mild steel requires precise parameter settings. Charts provide recommended amperage ranges based on material thickness. These starting points should be adjusted based on technique and travel speed for optimal results.
Amperage Settings for Mild Steel (Specific Thicknesses)
When TIG welding mild steel, amperage is paramount, directly impacting weld penetration and quality. Charts offer specific amperage guidelines based on material thickness, typically ranging from thin sheets to thicker plates. These values serve as a starting point. Fine-tuning is often necessary, considering factors like joint type, travel speed, and welder technique. For example, welding 0.8mm mild steel may require a lower amperage compared to 3mm steel. Remember that these charts offer reference points; always test and adjust for optimal weld results. Precise amperage control minimizes defects and maximizes weld integrity in mild steel applications.
TIG Welding Parameter Charts: Stainless Steel
Stainless steel TIG welding requires specific parameter charts. These charts detail amperage, voltage, and gas flow for various stainless steel grades. They help achieve clean, corrosion-resistant welds and are essential for quality results.
Amperage Settings for Stainless Steel (Specific Thicknesses)
When TIG welding stainless steel, amperage settings are crucial and directly linked to material thickness. Thinner stainless steel requires lower amperage to prevent burn-through, while thicker pieces need higher amperage for adequate penetration. Consulting a TIG welding chart tailored for stainless steel is highly recommended. These charts provide a starting point for amperage settings based on specific thicknesses, and adjustments can be made based on technique and observed weld behavior. Remember, these charts offer a baseline, and testing parameters before starting any welding project is always advised to ensure optimal results and prevent material damage.
TIG Welding Parameter Charts: Aluminum
Aluminum TIG welding demands specific parameter charts. These charts dictate amperage ranges, gas flow, and frequency settings. Aluminum’s heat sensitivity requires precise control to prevent burn-through and ensure strong, clean welds.
“Hot and Fast” Welding Approach for Aluminum
The “hot and fast” approach for aluminum TIG welding emphasizes high amperage and rapid travel speed. This minimizes heat input, preventing distortion and burn-through due to aluminum’s high thermal conductivity. Parameter charts guide welders in selecting appropriate amperage ranges for specific aluminum thicknesses.
Faster travel speeds further reduce heat buildup, resulting in cleaner welds with less porosity. This technique requires precise control and coordination but yields superior results on aluminum. It differs significantly from welding mild steel, where slower speeds are typical.
Tungsten Electrode Selection and Preparation
Tungsten electrode selection is critical for TIG welding. Proper preparation, including grinding the tip, ensures arc stability and weld quality. Different electrode types suit various materials and welding currents, impacting weld penetration and bead profile.
Electrode Diameter and Tip Preparation
Selecting the correct tungsten electrode diameter is crucial for TIG welding, influencing current carrying capacity and arc focus. A smaller diameter provides a more concentrated arc, ideal for intricate work. Tip preparation, achieved through grinding, shapes the electrode for specific welding applications. A pointed tip enhances arc starting and penetration on steel, while a blunted or balled tip is preferred for aluminum. Proper grinding techniques prevent contamination and ensure consistent weld quality. Different grinding angles affect the arc characteristics. Always consult charts for optimal electrode selection and preparation based on material type, thickness, and welding parameters.
Filler Metal Selection Guidelines
Choosing the correct filler metal is vital for strong, quality TIG welds. Guidelines emphasize matching filler composition to the base material. Selection charts aid in determining the appropriate alloy and diameter for optimal results.
Choosing the Right Filler Rod Composition and Size
Selecting the appropriate filler rod is crucial for TIG welding success. The filler rod’s composition must be compatible with the base metal to ensure a strong, durable weld. Charts and guides provide recommendations based on material type, such as matching stainless steel filler to stainless steel base metal and aluminum filler to aluminum base metal.
Furthermore, the diameter of the filler rod should correspond to the thickness of the materials being joined and the desired weld bead size. Thicker materials typically require larger diameter filler rods. Consulting a welding chart PDF offers specific guidelines.
Online TIG Welding Calculators and Resources
Online TIG welding calculators and resources offer convenient tools for determining optimal welding parameters. These resources often provide recommendations for amperage, voltage, gas flow, and electrode selection based on material type and thickness.
Miller’s TIG Welding Calculator
Miller’s online TIG welding calculator is a valuable resource for welders seeking recommended parameters. This calculator provides suggestions for shielding cup size and flow rate, tailored to various weld joint types, materials, and thicknesses. By inputting specific details about the welding project, users can receive data-driven parameter recommendations to optimize their TIG welding process. This tool helps welders achieve precise and high-quality welds by providing a reliable starting point for their settings. The calculator simplifies parameter selection, saving time and reducing the risk of errors during setup and execution.
CK Worldwide’s Technical Specifications and Charts
CK Worldwide offers technical specifications and charts, providing information similar to Miller’s calculator. These resources include essential data for TIG welding, such as suggested parameters. CK Worldwide also provides a useful guide for shield gas flows and current settings, which aids in optimizing the welding process. Welders can use these charts and guides to determine appropriate settings for different materials and thicknesses, ensuring precise and high-quality welds. The availability of these resources enhances the welder’s ability to achieve consistent and reliable results in various TIG welding applications.
Troubleshooting Common TIG Welding Issues
Addressing TIG welding issues requires understanding parameter adjustments. Optimal weld quality hinges on proper settings. By consulting resources and guides, welders can diagnose and resolve common problems, ensuring consistent and high-quality results.
Adjusting Parameters for Optimal Weld Quality
Achieving optimal weld quality in TIG welding involves meticulous parameter adjustments. Assessing weld appearance is crucial, looking for signs of porosity, undercut, or excessive heat input. Based on these observations, welders must fine-tune settings like amperage, gas flow, and travel speed. Adjusting amperage ensures proper penetration without overheating. Shielding gas flow impacts weld cleanliness and prevents oxidation. Travel speed affects bead width and heat distribution. Consulting welding charts and resources, such as those from Miller or CK Worldwide, provides valuable guidance. Continuous evaluation and adjustment are key to consistent, high-quality TIG welds, adapting to the specific material and joint configuration.