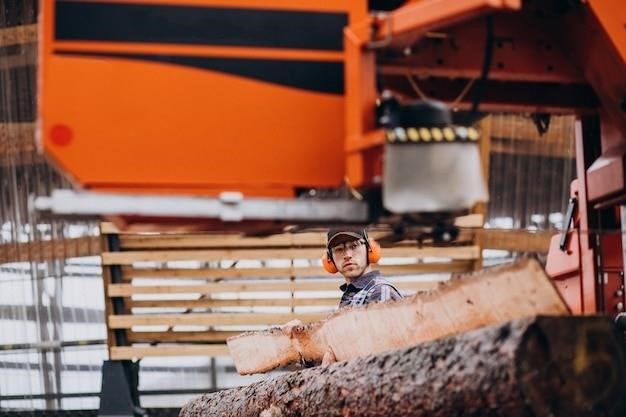
sawmill blade guides
Sawmill Blade Guides⁚ A Comprehensive Overview
Sawmill blade guides are crucial for precise cutting and efficient operation. They maintain blade alignment, preventing wandering and ensuring straight cuts. Proper guide selection and maintenance significantly impact sawmill performance and blade lifespan, ultimately boosting productivity and minimizing waste. Various guide types cater to different sawmill models and applications, from simple roller guides to sophisticated adjustable systems. Understanding these systems is paramount for optimal results.
Types of Sawmill Blade Guides
Sawmill blade guides come in various designs, each with its own advantages and disadvantages. The most common type is the roller guide, utilizing rollers to support the blade and minimize friction. These are often found in portable sawmills like those from Cook’s and Woodmizer, providing a balance of simplicity and effectiveness. Adjustable blade guides offer greater precision and versatility. These systems allow for fine-tuning blade alignment, compensating for variations in log size and shape. They are particularly beneficial for high-precision cutting applications. Some manufacturers, such as Norwood, incorporate advanced adjustable guide technology for enhanced accuracy and control. Beyond these, specialized guides exist, often tailored to specific sawmill brands or models. Choosing the right guide type depends heavily on the sawmill’s size, capacity, and the desired level of cutting precision. The material used in construction, whether steel, carbide, or ceramic, also plays a significant role in durability and performance. Proper selection of guides is crucial to maximize sawmill efficiency and minimize blade wear.
Roller Guides⁚ Functionality and Maintenance
Roller guides, prevalent in many sawmill designs including Cook’s and Woodmizer models, function by using rollers to support the blade’s weight and reduce friction during cutting. These rollers, often case-hardened and precision-ground for longevity, minimize blade deflection and ensure straight cuts. The system’s effectiveness hinges on proper maintenance. Regular lubrication is crucial; greasable bearings, often included with Cook’s guide systems or available separately (as with their zerk bolt option), extend roller life and minimize wear. Inspect rollers frequently for signs of damage, such as pitting or excessive wear. Replace worn or damaged rollers promptly to prevent blade misalignment and potential accidents. Alignment is critical; misaligned rollers can cause the blade to bind, leading to premature wear and decreased cut quality. A correctly aligned system ensures smooth blade movement, contributing to cleaner cuts and improved overall sawmill performance. Addressing maintenance needs proactively prevents costly downtime and ensures continued efficient operation.
Adjustable Blade Guides⁚ Benefits and Applications
Adjustable blade guides offer superior control and versatility compared to fixed roller systems. These systems, often featuring stainless steel V-rollers and machined aluminum arms (as seen in premium designs), allow for precise blade alignment adjustments. This adaptability is particularly beneficial when working with varying wood types or thicknesses, ensuring optimal blade tracking regardless of material characteristics. The ability to fine-tune guide positioning enhances cut accuracy and minimizes blade deflection, leading to straighter, cleaner cuts and reduced waste. Applications range from portable sawmills like Woodland Mills HM122 and HM126 (2020 and newer models) to larger industrial setups. However, compatibility varies, with some adjustable guide systems designed specifically for particular sawmill brands or models (note incompatibility with older Woodland Mills models). The improved control offered by adjustable guides results in increased productivity and enhances the overall quality of the lumber produced. Investing in a high-quality adjustable system can significantly improve a sawmill’s efficiency and output.
Guide Systems for Specific Sawmill Brands (e.g., Cook’s, Woodmizer)
Sawmill blade guide systems are often brand-specific, requiring careful consideration when selecting replacement parts or upgrades. Cook’s sawmills, for example, utilize case-hardened and precision-ground roller guides, often featuring greasable bearings for smooth operation and extended lifespan. These guides are compatible with many Cook’s models, including the MP-32 and HD-3238, and sometimes fit Woodmizer sawmills as well. Woodmizer, a prominent sawmill manufacturer, offers its own proprietary guide systems, designed to work seamlessly with their various sawmill models. Understanding the specific guide requirements for each brand is vital for maintaining optimal performance and preventing premature wear. Incorrect guide selection can lead to misalignment, reduced cut quality, and accelerated blade wear. Always refer to the manufacturer’s specifications and diagrams to ensure compatibility and proper installation. Replacement parts should be sourced from authorized dealers to guarantee authenticity and performance. The use of generic or improperly fitting guides can severely impact both the efficiency and longevity of your sawmill.
Choosing the Right Guide System for Your Sawmill
Selecting the appropriate blade guide system for your sawmill is critical for optimal performance and longevity. Consider the sawmill’s make and model; compatibility is paramount. Consult the manufacturer’s specifications to ensure proper fit and functionality. Factors such as blade width, thickness, and the type of wood being processed will also influence the choice of guide system. Roller guides, known for their smooth operation and durability, are widely used, but adjustable guides offer greater precision for various cutting tasks. The material of the guide is also important; stainless steel or carbide options offer superior wear resistance compared to standard steel. Evaluate your budget; higher-quality guide systems typically command a higher price but may ultimately save money through increased blade life and reduced downtime. Assess your maintenance capabilities; some systems require more frequent lubrication or adjustment than others. Prioritize safety; choose a system that offers secure blade control and minimizes the risk of accidents. Thorough research and careful consideration of these factors will ensure the selection of a guide system that optimizes your sawmill’s efficiency and productivity.
Maintaining and Replacing Sawmill Blade Guides
Regular maintenance is crucial for optimal sawmill performance. Inspect guides frequently for wear, lubricate moving parts, and promptly address any alignment issues. Replacing worn or damaged guides prevents blade damage and ensures accurate cuts, maximizing sawmill efficiency and safety.
Regular Inspection and Lubrication
Regular inspection and lubrication of sawmill blade guides are essential for maintaining optimal performance and extending their lifespan. A thorough inspection should be conducted before each use, checking for any signs of wear, damage, or misalignment. Look for excessive wear on rollers, cracks or deformation in guide components, and any signs of binding or friction. Pay close attention to the guide system’s mounting hardware, ensuring all bolts and fasteners are securely tightened. Loose hardware can lead to misalignment and premature wear. Lubrication is crucial for reducing friction and wear on moving parts. Use a high-quality lubricant specifically designed for sawmill applications, avoiding excessive lubrication which can attract sawdust and create a messy operation. Apply lubricant to all moving parts according to the manufacturer’s recommendations. The frequency of lubrication will depend on the type of guide system and the intensity of use. Regular maintenance and timely lubrication will significantly improve the longevity and efficiency of your sawmill blade guides. Remember to always consult your sawmill’s manual for specific maintenance instructions. By adhering to a regular inspection and lubrication schedule, you will ensure your sawmill continues to deliver precise, efficient cuts. This proactive approach will minimize downtime and maximize your overall productivity.
Troubleshooting Common Guide Issues
Troubleshooting sawmill blade guide issues often involves systematic checks and adjustments. A common problem is blade wandering, which might indicate misaligned guides, worn rollers, or uneven tension. Begin by carefully inspecting the guides for any signs of damage or wear, such as excessive scoring or deformation on roller surfaces. Check the mounting hardware to ensure everything is securely fastened; loose components can easily lead to misalignment. If the blade repeatedly climbs or dives, the guide system may need adjustment. This often requires fine-tuning the height and angle of the guides. Consult your sawmill’s manual for precise adjustment procedures. Another potential issue is increased blade friction, which can manifest as increased cutting effort or overheating. Insufficient lubrication is a frequent culprit, so apply lubricant to the designated areas. If the problem persists, the guides themselves may be worn or damaged, requiring replacement. Remember, worn or damaged guides can lead to inaccurate cuts, reduced blade life, and even potential safety hazards. Always prioritize safety when working with sawmill equipment. If you are unable to resolve the issue independently, consult a qualified technician or refer to the manufacturer’s troubleshooting guide for more detailed assistance. Addressing guide problems promptly will ensure the efficient and safe operation of your sawmill.
Replacing Worn or Damaged Guides
Replacing worn or damaged sawmill blade guides is a crucial maintenance task ensuring optimal cutting performance and blade longevity. Before starting, always disconnect the power source to the sawmill, ensuring complete safety. The process typically involves removing the old guides, which may involve unscrewing fasteners or releasing clamps depending on the guide system. Take note of the guide’s orientation and any specific alignment marks before removal to aid in correct reinstallation. When selecting replacement guides, ensure compatibility with your sawmill model and blade size. Using incorrect guides can lead to misalignment and damage. Once the old guides are removed, carefully clean the mounting surfaces, removing any debris or old lubricant. Install the new guides precisely aligning them according to the manufacturer’s instructions or any existing alignment marks. Securely tighten all fasteners, ensuring that the guides are firmly fixed in place. After installation, lubricate the guides as per the manufacturer’s recommendations. This lubrication helps reduce friction and extends the life of the replacement guides. Following installation, test the sawmill, observing the blade’s operation closely. Any signs of misalignment or erratic blade movement require immediate attention. If problems persist after replacement, re-check the installation process and consult your sawmill’s manual or seek assistance from a qualified technician. Regular inspection and timely replacement of worn guides are key to maintaining the precision and efficiency of your sawmill.
Guide System Alignment and Adjustment
Precise alignment and adjustment of the sawmill blade guide system are critical for achieving accurate cuts and maximizing blade life. Improper alignment can lead to blade wander, resulting in inaccurate cuts and increased risk of blade breakage. Begin by ensuring the sawmill is properly leveled and the log is securely clamped. Many systems utilize adjustment screws or bolts to fine-tune the guide’s position relative to the blade. These adjustments typically allow for both vertical and horizontal fine-tuning. Start by checking for any visible misalignment; the guides should be parallel to the blade and properly spaced. Use a straight edge or measuring tools to verify alignment if necessary. Small adjustments should be made incrementally, observing the effect on blade tracking after each adjustment. Over-adjustment can lead to further misalignment. For systems with multiple guides, ensure consistent spacing and parallelism between them. The guides should be positioned to provide even support along the blade’s entire length, preventing any undue stress or pressure points. Regular checks for alignment are crucial, especially after significant use or blade changes. If you encounter persistent alignment issues, consider consulting your sawmill’s manual or seeking guidance from an experienced sawmiller. Remember, proper alignment is a key factor in achieving consistently high-quality cuts and maintaining overall sawmill efficiency. Accurate alignment minimizes blade wear and tear, ultimately contributing to cost savings and extended equipment lifespan.
Impact of Blade Guides on Sawmill Performance
Optimal sawmill blade guides significantly enhance cut quality, precision, and blade longevity. They contribute to increased efficiency and overall sawmill productivity by minimizing waste and maximizing output. Properly functioning guides ensure smooth operation and reduce the likelihood of costly repairs or downtime.
Improving Cut Quality and Accuracy
High-quality sawmill blade guides are instrumental in achieving precise and accurate cuts. By maintaining consistent blade alignment, they prevent the blade from wandering or deviating from the intended cutting path. This results in straighter, cleaner cuts with minimal deviation, reducing the need for additional processing or finishing. The improved accuracy translates directly into less material waste and higher-quality lumber. The use of correctly adjusted and maintained guides minimizes the risk of producing boards with uneven surfaces, crooked edges, or other imperfections that might necessitate rework or rejection. Investing in robust and properly functioning guides is an investment in superior lumber quality and reduced operational costs. The precision offered by these guides allows for thinner kerfs, further reducing material loss and optimizing yield. This precision is particularly crucial when processing valuable or high-demand wood species, where maximizing yield and minimizing defects is paramount. In essence, superior blade guides directly contribute to a significant improvement in the overall value and marketability of the finished product.
Enhancing Blade Lifespan and Efficiency
Properly functioning sawmill blade guides play a crucial role in extending the lifespan of saw blades and improving overall cutting efficiency. By ensuring consistent blade tracking and preventing unwanted vibrations or side-to-side movement, guides significantly reduce the friction and stress on the blade. This minimizes the wear and tear on the teeth, preventing premature dulling and damage. A well-maintained guide system allows the blade to cut smoothly and efficiently, requiring less power and reducing the risk of blade breakage; This translates into lower operating costs associated with frequent blade replacements and reduced downtime for blade changes. Moreover, the consistent cutting action produced by properly aligned guides results in cleaner cuts, reducing the need for additional sharpening or repairs. The improved blade life and efficiency also contribute to increased sawmill productivity, allowing for a greater volume of lumber to be produced in a given timeframe. Investing in high-quality guide systems and adhering to regular maintenance practices is therefore a cost-effective strategy for optimizing sawmill operations and maximizing return on investment.
Optimizing Sawmill Productivity
Sawmill blade guides are instrumental in optimizing overall productivity. Efficient guides ensure smooth, consistent cutting, minimizing downtime caused by blade adjustments or replacements. Reduced blade wear translates directly into fewer interruptions for sharpening or changing blades, keeping the sawmill running continuously. Precise blade tracking, facilitated by well-maintained guides, leads to higher lumber yield per log, reducing waste and maximizing profitability. The ability to maintain consistent cutting speed and accuracy, thanks to properly aligned guides, increases the volume of lumber produced in a given time frame. This enhanced throughput directly impacts the sawmill’s output and revenue generation. Furthermore, the reduction in blade breakage and repairs, a direct result of using and maintaining quality guides, contributes to significant cost savings. By preventing log jams and ensuring consistently straight cuts, the guides contribute to a more efficient workflow, allowing the sawmill crew to focus on other tasks. In summary, investing in and maintaining optimal blade guides is a crucial step towards achieving maximum sawmill productivity and profitability.